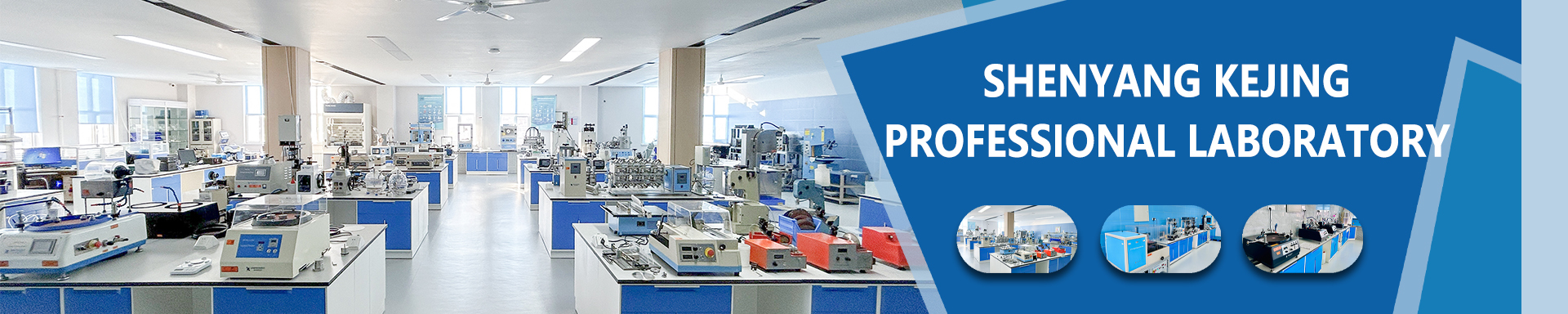
How to Coat Silicon Wafers Using the PTL-NMB Nanometer Grade Thermostatic Dip Coater?
2025-01-27 15:30In modern material research and semiconductor manufacturing, thin film preparation and coating technology are crucial. Especially in the field of thin film coating with nanometer precision, PTL-NMB nanometer grade thermostatic dip coater, as a precision equipment, has become an important tool in research and industrial applications. This article will introduce in detail how to use PTL-NMB nanometer puller to coat silicon wafers.
The main purpose of this experiment is to use nanometer grade thermostatic dip coater to coat silicon wafers on both sides and observe the deposition of thin films on the surface of silicon wafers. As an important substrate in semiconductor research, the quality of the surface coating of silicon wafers directly affects the subsequent process effect. Therefore, the use of precisely controlled coating methods, such as nanometer pull coater, can make the coating uniform and precise.
Experimental steps:
1. Silicon wafer cleaning:
Before the experiment begins, the silicon wafer needs to be thoroughly cleaned. Soak the silicon wafer in deionized water to keep the sample surface free of external contaminants. Then, remove the water stains with acetone, clean it thoroughly with deionized water, and use PCE-6V plasma cleaner to plasma etch the silicon wafer for 10 minutes. After etching, the silicon wafer should avoid being exposed to the air for more than 30 minutes, otherwise the surface state may fail and affect the adhesion of the film.
2. Parameter setting:
Pour the liquid material into a 150ml material cup and mount the silicon wafer on the sample fixture to prepare for coating. In the experiment, the silicon wafer is first completely immersed in the solution. Then, the pulling speed is set to 100nm/s and the pulling height is set to 50mm on the nanometer grade thermostatic dip coater. According to calculations, the entire pulling process takes about 139 hours.
3. Coating process:
During the coating process, the silicon wafer is controlled by the puller, and the solution is gradually pulled out from the surface of the substrate to form a uniform film. Because the working speed of the puller is very fine, the deposition process of the film is very stable, and the film finally coated on the surface of the silicon wafer has good uniformity and consistency.
By using the nanometer grade thermostatic dip coater, researchers can accurately coat the surface of the silicon wafer on both sides and control the thickness and quality of the film. The experimental results show that during the coating process, the deposition of the film is uniform and meets the nanometer-level precision requirements, making it suitable for research on semiconductors and nanomaterials.