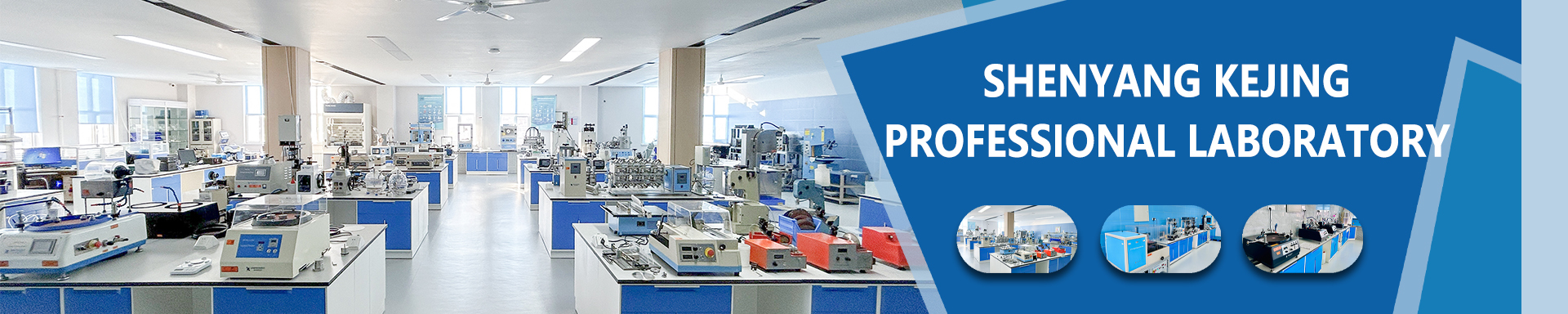
Polishing Machine Troubleshooting And Maintenance
2024-10-22 15:40In the production and processing process, the normal operation of the UNIPOL-800M multi-point mechanical pressure grinding and polishing machine is crucial to ensure the quality of the workpiece. However, in daily use, various problems may occur, affecting the processing effect of the workpiece. This article summarizes several common faults of automatic pressure grinding and polishing machine and the corresponding solutions to help manufacturers maintain equipment in a timely manner and improve production efficiency.
1. The polishing wheel does not run.
Cause: Common reasons for the polishing wheel not running include motor failure or cylinder abnormality.
Solution: First, you can try to press the reset button to perform the reset operation. If the problem is still not solved, use a multimeter to check whether the motor is missing phase or open circuit, and replace the motor if necessary. To ensure the normal operation of the pneumatic components.
2. Uneven polishing.
Cause: Uneven polishing of the polishing cloth wheel or uneven polishing pressure may cause uneven polishing of the workpiece.
Solution: To ensure the polishing effect, the polishing cloth wheel should be leveled regularly, and the polishing pressure of each point should be adjusted to make the pressure on the workpiece surface uniform, thereby improving the polishing quality.
3. Workpiece deformation.
Cause: Thin workpieces are easily affected by clamping force during grinding due to their poor rigidity, resulting in deformation.
Solution: It is recommended to use a magnetic suction cup and pad a thin rubber sheet between the workpiece and the suction cup to reduce clamping deformation. In addition, an elastic clamping mechanism is used to enable the workpiece to be positioned and clamped in a free state.
The maintenance of automatic grinding and polishing machine plays a vital role in the production process. Correct maintenance measures can not only extend the service life of automatic grinding and polishing machine, but also ensure the processing quality of the product. By understanding and mastering the solutions to these common problems, you can more efficiently deal with equipment failures in the production process and improve overall production efficiency and workpiece quality.