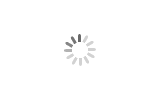
Laboratory Small Extrusion Film Coating Machine
Brand Shenyang Kejing
Product origin Shenyang, China
Delivery time 10 working days
Supply capacity 50 sets
1. The thin film preparation coating machine is small in size and adopts a split design. Each part can be placed in different positions.
2. The thin film preparation coating machine uses a 24V power supply and can be used in a glove box
3. The thin film preparation coating machine is easy to set up, plug and play, and does not require compressed gas or vacuum pipelines.
Introduction of thin film preparation coating machine:
MSK-AFA-SD70-II Split laboratory coating machine is a 24V extrusion coating machine, mainly used in glove boxes. The equipment is used for surface coating of sheet substrates and is coated by slit extrusion. The Split laboratory coating machine is mainly composed of an extrusion die, a coating platform, a feeding system and a control system, and is mainly used for laboratory research and development. The Laboratory Thin Film Coater is mainly used for surface coating of sheet substrates in the fields of lithium battery substrates, OLEDs, solar photovoltaic films and polymer conductive films, and for the preparation of perovskite deposition films.
Advantages of Small laboratory coating equipment:
1. Small laboratory coating equipment has high uniformity---the hanger-type solution distribution design has uniform flow rate, so the Split laboratory coating machine can obtain highly uniform coatings, which are suitable for solvents of various viscosities. The stainless steel slot die head is compatible with a wide range of liquid materials.
2. Variable liquid channel thickness---stainless steel gaskets of different thicknesses or widths can be replaced to change the thickness or width of the slot die channel. Multiple gaskets can also be inserted to increase the thickness of the liquid channel.
3. Zebra stripe coating--parallel stripes can be coated by making the stainless steel gasket into a zebra stripe shape.
4. Uniform flow and thickness---using a micro-injection pump with adjustable flow rate for liquid supply, the user can accurately control the amount of solution entering the slit die system through the control system of the Small laboratory coating equipment, so as to accurately and repeatably control the thickness of the deposited film.
5. Small laboratory coating equipment can be temperature controlled---the substrate temperature can be adjusted between room temperature and 120°C. Controlling the substrate temperature by heating to reduce surface tension can improve the wettability of the solution, while the drying rate can also change the nanostructure of the deposited film.
6. Wide range of substrate speed settings---the operating platform can move smoothly and continuously. The motor moves at speeds as low as 0.1mm/s to as high as 10mm/s.
7. The Small laboratory coating equipment can be precisely positioned---the position between the platform and the coating head can be precisely adjusted by using a three-point leveling system and a high-precision micrometer. Fine alignment allows the system to achieve height changes as low as 1um/cm within the platform travel range.
8. Coating head height control---Two micrometers are set above the coating head frame to adjust the position between the coating head and the platform. By adjusting the height of the slit die of the Small laboratory coating equipment, the stability of the meniscus is improved and the wet film thickness is changed.
Technical parameters of thin film preparation coating machine:
Product Model | MSK-AFA-SD70-I |
Product Name | MSK-AFA-SD70-II thin film preparation coating machine |
Technical Parameters | |
Coating head width | 70mm (Other sizes can be customized, maximum width ≤ 100mm) |
Maximum heating temperature | 120℃ |
Platform itinerary | 1-100mm |
Minimum stage speed | 0.1mm/s |
Maximum stage speed | 10mm/s |
Injection pump MIN feed speed | MIN0.001mm/s |
Injection pump MAX feed speed | MAX1mm/s |
MAX substrate thickness | 10㎜ |
Platform flatness | <50μm |
Power supply | 220V AC 50Hz |
Device host size | 220mmX330mmX260mm |
Device control box size | 390mmX340mmX170mm |
Injection pump size | 65mmX250mmX50mm |
Size Details | ![]() |
Customizable integrated machine | ![]() |
Process Introduction of Split laboratory coating machine:
Process description: The liquid enters the extrusion coating head through the injection pump, and the extrusion coating head applies the liquid to the surface of the substrate to form a coating while moving.
Material Requirements of Split laboratory coating machine:
1. Substrate requirements:
Project | Parameter |
Substrate requirements | Copper foil, aluminum foil, glass, PTFE, PET and other sheet substrates |
Size | L100mm*W100mm*H10mm(max) |
2. Slurry requirements:
Project | Liquid |
Viscosity | Max.1000 cps (below, depending on the slurry characteristics) |
Device Specifications of Split laboratory coating machine:
1、Equipment body:
NO. | Project | Device Specifications | Remark |
1 | Type | Split structure | |
2 | Color | Black, white, silver |
2、Feeding unit:
NO. | Project | Device Specifications | Remark |
1 | Type | Automatic feeding, manual replacement of syringe barrel | |
2 | Adjustment | Touch screen + button operation | |
3 | Syringe | Compatible with 10ml, 20ml and 30ml syringes |
3、Coating unit:
NO. | Project | Device Specifications | Remark |
1 | Type | Automatic coating | |
2 | Extrusion die | Single cavity structure | Customizable |
3 | Die head gasket | Finely rolled stainless steel C-type gasket, opening width 50mm | Customizable |
4 | Height adjustment | Micrometer adjustment, digital display |
4、Heating unit:
NO. | Project | Device Specifications | Remark |
1 | Coating platform | Stainless steel platform | |
2 | Heating source | Heating element, built-in |
Logistics:
Quality Commitment:
Our company guarantees that the equipment provided is brand new, unused, and fully meets the quality, specification and performance requirements specified in the contract, and that our equipment should have satisfactory performance under correct installation, correct use and maintenance conditions and during its service life.