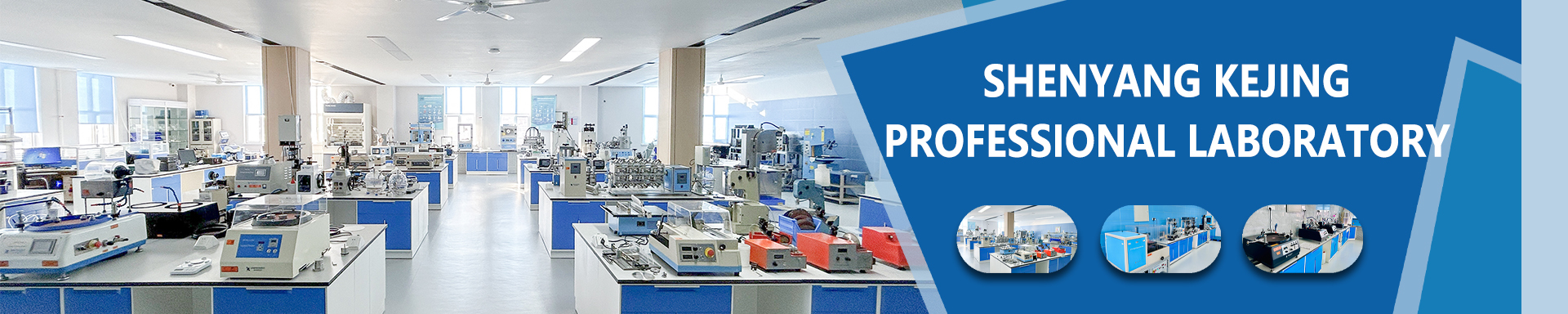
Do You Know The Importance Of Operating The Metallographic Electro Polishing Machine Safely?
2024-12-03 15:30The EP-1060 electrolytic polisher has become an indispensable tool in metallographic specimen preparation due to its excellent functionality and portability. However, in order to better utilize the equipment performance, while ensuring the safety of laboratory personnel and the long-term use of the equipment, it is particularly important to operate and maintain the equipment correctly. The following are key considerations for the operation and maintenance of electrolytic polishers and etchers for metallography. Let's take a look!
1. Operation requirements:
Stable placement: The instrument should be placed on a flat workbench for operation to ensure stability.
Suitable environment: Operate in an allowable working environment with a temperature range of -10℃ to +40℃ and relative humidity below 90%.
Safe start: The power can only be turned on after the connection is completed to avoid equipment failure or safety hazards caused by improper wiring.
2. Precautions for use:
Ventilation and heat dissipation: There must be sufficient ventilation space around the electrolytic polishers and etchers for metallography, and no items should be stacked in the front, sides, and back.
Comply with the rated values: The electrolytic polishers and etchers for metallography must be used within the rated voltage and current range. Illegal operation May cause electric shock or fire risks.
Reasonable selection of wires: When connecting the metallographic electro polishing machine, standard wires must be used, or wires that meet the rated load must be selected to ensure safe operation.
Short circuit protection: The metallographic electro polishing machine has a current limiting protection function, but when a short circuit or overload occurs, the power should be turned off immediately and the fault should be eliminated.
Clean up after the experiment: After the experiment, the electrolyte needs to be recovered into a special container, the beaker and equipment need to be cleaned, and stored in a ventilated and dry place.
Protective measures: Most electrolytes are highly corrosive substances, and protection must be done during operation to avoid human contact.
3. Maintenance and care:
Surface cleaning: Wipe the dust on the surface of the metallographic electro polishing machine regularly with a lint-free cloth. The cloth should not be too wet to avoid damaging the equipment.
Power-off protection: After the equipment is out of use, the power should be turned off in time to avoid damage caused by sudden power-on.
Pay attention to the environment: Avoid placing the electro etching machine for metallurgical in a high temperature and dusty environment to avoid affecting the performance of the equipment.
The electro etching machine for metallurgical not only greatly improves the experimental efficiency with its integrated electrolytic polishing and corrosion functions, but also helps users reduce experimental risks and extend the life of the equipment through scientifically designed operating specifications and perfect maintenance guidance. Whether in factories, universities, or scientific research laboratories, the electro etching machine for metallurgical can provide reliable support for sample preparation. In order to better support scientific researchers and laboratory staff, we sincerely welcome user feedback and suggestions to continuously improve equipment performance and user experience.